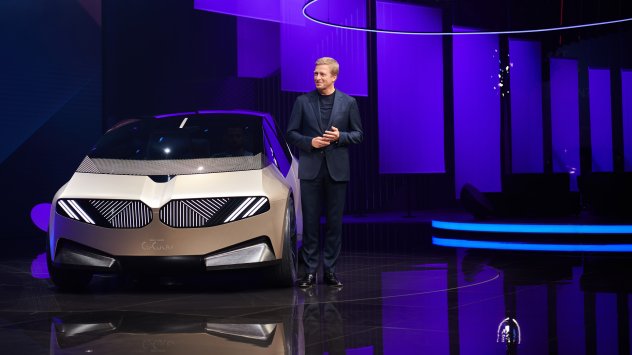
By KONSTANTIN TOMOV
Covid-19 messed things up a bit. If it weren't for the virus, the word of 2021 would probably be 'Greenwashing', instead of 'Vax'. This term refers to false or misleading information about the supposed environmental merits of a product, service or company. From year to year, greenwashing is gaining more and more threatening proportions: another proof that even the most rational, practical and well-intentioned idea for the future is powerless when marketing departments intervene in the game.
You may be surprised, but the term is not new. It was first used by the American environmentalist Jay Westerveld back in 1986, in response to the practice of large hotels at the time to encourage their customers to use the same towels for days. A practice that, as Westerveld rightly suspected, had little to do with caring for nature, but very much so with the desire of hotels to reduce their costs.
Nowadays, 'greenwashing' - or, as Bulgarians say, 'green caviar' - is a growing phenomenon that affects all sectors from food production to telecommunications. But nowhere is this more obvious than in the automotive industry.
Fifteen years ago, only a few companies showed any interest in electric drivetrains: BMW, Renault-Nissan, Mitsubishi, GM. Their efforts were mostly ridiculed by their competitors. Today, there is virtually no manufacturer who has not announced a course towards electrification. "Eco", "green" and "sustainable" have long replaced the classic marketing mantras such as "fast", "powerful" and "comfortable". But, with very few exceptions, behind the green facade lies an opaque grey area.
The dirty birth of electric cars
There is nothing ecological in the very act of replacing the internal combustion engine (ICE) with an electric motor and a battery. The opposite is true: the production of an electric car, if we include the extraction of raw materials, emits significantly more harmful emissions than the production of a car with a petrol or diesel engine. Exactly how much more, is impossible to say: it depends on the design and efficiency of the car, the production methods, the subcontractors and where the raw materials for the main components come from.
Car companies say they are striving for more sustainable production, but how many of them are doing it with enough enthusiasm?
Here's one exception: the BMW Group. The German giant has not only declared sustainability as its main goal but has also hired independent auditors to assess its progress in this regard. " We are making the independent testing of our sustainable activities even more stringent than before. Because credibility comes with transparency," said CEO Oliver Zipse.
Effective - or fast?
Of course, electric cars have one serious advantage: even if their production emits more harmful emissions than the production of internal combustion cars, this is further compensated by their daily usage. The electric drivetrain has a much higher efficiency than ICE (on average about 70-80% efficiency, while that of the most modern gasoline engines barely exceeds 40%). But even in this respect, electric cars are far from equal. Some of the pioneers in this field, such as GM with its already forgotten EV1 or BMW with i3, tried to make their electric cars as efficient as possible - with good aerodynamics, lightweight construction, reduced dynamic performance at the expense of lower energy consumption. Others, led by Tesla, relied more on the dynamics and amazing capabilities of electric motors for fast acceleration. Needless to say, which approach has been better accepted by the market.
The electric car: clean in France, but not in Poland
There is another problem with the environmental friendliness of electric cars, which has been talked about for a long time, but which has rarely been measured with specific numbers. It is about the origin of the energy with which they are charged. "If you drive an electric MINI Cooper SE in Poland, its average emissions of CO2 will be around 110 grams per kilometre, because the electricity is mainly from coal," explains Andreas Klugenscheid, head of government relations for Europe at the BMW Group. 110 grams are the emissions of a normal petrol car. Some more compact cars - both petrol and diesel - emit noticeably less. But Klugenscheid's example doesn't stop there: "If you move the same MINI a few hundred kilometres west to Berlin, its emissions will drop to about 60 grams per kilometre. And if you travel another 500 kilometres to France, they will be only 5 grams, because of nuclear energy". That is, in countries with polluting power generation, the electric car is not a step forward in environmental terms. It can even be a step backwards.
Climate-neutral plants
Of course, this applies to electric cars, which are produced in the old way. BMW's development shows that this is not mandatory. More than a decade ago, the Germans began to rethink their production cycle. The American plant in Spartanburg has drastically reduced water use since. All in-house transport at Landshut is now electric. The Munich and Dingolfing factories use only hydroelectric power. In Leipzig, they rely on wind energy, in the Mexican plant in San Luis Potosi - on solar. Oliver Zipse claims that in the very foreseeable future all BMW plants will be climate-neutral.
New supply chains
Now the same goal is being transferred to suppliers - they will also have to guarantee and prove sustainable production. We ask Andreas Metzner, BMW's spokesperson for sustainable development, whether this is leading to any shifts in the supply chain. "Weekly. Even daily," Metzger replies. "We closely monitor our suppliers. But we also offer incentives: when there are good results, when they restructure their production networks according to our requirements, the reward is long-term, secure contracts for 5-10 years." Metzger admits that some of BMW's existing partners have refused such a transformation, and have turned to other customers. "We prefer to buy more expensive but to have full control from the mine to the final product. People who deal with BMW orders now add to the two key parameters - price and quality - a third, sustainability. "The figures for our sustainable actions are given the same importance as our financial figures," said Nicholas Peter, the company's CFO.
Eco apples from New Zealand
The length of the supply chain itself is another issue that 2021 has highlighted. With rising transport prices, the supply of components from the other side of the world is no longer so economically viable. Which can give an additional trump to manufacturers such as Bulgaria, which in the last decade has developed a very serious automotive parts industry. Delivering from Bulgaria to Germany is obviously cheaper - and more sustainable - than delivering from China to Germany, for example. But here, too, summaries do not work because there are too many special cases. For some raw materials, such as cobalt, there is no way to shorten the supply chain simply because they are not available nearby, Metzger says. And I remember a story from a few years ago: a lecturer on sustainable development asked his audience which was more environmentally friendly for Germans - to eat apples grown in Germany, or imported from New Zealand. It turned out that the answer is not so obvious, and depends on the season. In winter, German apples are from greenhouses and are grown with much more emissions than it costs to transport New Zealand apples from the other side of the world. Each individual supply chain must be carefully studied to avoid such errors.
The solution: Circular car
Finally, we come to perhaps the most significant argument against the electrification of transport: that replacing existing cars with electric ones will be a colossal source of new emissions. In many cases, it is more environmentally friendly to use an old, existing machine, no matter how polluting, than to build a new one.
By the way, the same is true for the textile industry, and consumer electronics, and almost every other sector of the manufacturing economy. BMW recognizes this, and it is no coincidence that the key idea in their strategy for the future is the material cycle. At the last IAA Motor Show in Munich, the company presented the BMW i Vision Circular - a concept for a car made entirely of recyclable materials. Recycling is by no means new, of course - but the idea of a fully recyclable car is indeed revolutionary. Simply because at the moment we know how to recycle too few of our cars. Metal reuse is relatively easy. But reusing plastics, especially when it comes to combinations of different types of plastics with different temperature parameters, is a challenge. The automotive industry is gradually returning to natural materials that were abandoned a century ago, such as wood and wool. "We have not yet solved all the problems on the road. But we know that it is possible to make a car that is almost completely recyclable. It will take decades, but it still has to start somewhere," explains Andreas Metzger. "We just finally realized that we don't have endless resources, and that we need to find a way to live with the quantities we have. We need to create a circular approach in the whole industry, not just cars."